How reliable are you? Part 3: Reliably ever after
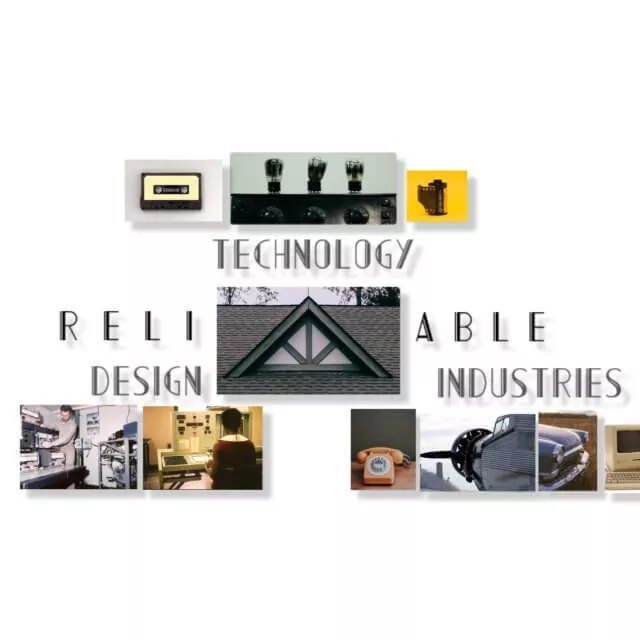
Welcome to the third and final part of the reliability blog series. I ‘ve already written about reliability prediction analysis and focused on different failures and calculation models. In this last part of the blog, I will continue to discuss the different standards and handbooks for reliability mentioned in ISO 26262, to compare the advantages and disadvantages of some of them and how to use them in practice.
Let’s start with IEC-TR-62380, a reliability prediction standard developed by the French industry to calculate the FIT rates for electronic systems. IEC-TR-62380 was in 2017 replaced by IEC 61709. The issue with that is IEC 61709 does not provide base failure rates for components, rather it provides models to calculate the failure rates. However, IEC-TR-62380 is still well known and used in the semiconductor industry e.g. IEC-TR-62380 calculation models were incorporated into the actual version (2018) of functional safety standard ISO 26262 (Part 11-Clause 4.6.2.1.1) and are used as basis for a model for reliability prediction of electronic components. In contrast to other standards, IEC-TR-62380 reliability prediction method considers not only the static temperatures, but also the temperature variations and the effects of mission profiles on an electronic system. It considers also the electric environment conditions (voltage and current overloads) for semiconductors.
The methodology of IEC-TR-62380 focuses on the maximum reliability of the component or system in the design phase considering different influence factors and is very popular with development engineers. The disadvantage of IEC-TR-62380 is that it is out-dated. It was published in 2004 by IEC (International Electrotechnical Commission), a revision has not yet been released, nor is one planned. Development in this area, especially in the semiconductor industry, brings some doubts about the applicability of this standard as is. Prediction calculation formula for IC packages for example are more or less reduced to a base failure rate, which was statistically evaluated, and the dimensions of it. The actuality of the base failure rate due to the different package innovations could be questioned if we think about the development of the semiconductor industry in the last 15 years. However, as mentioned above, there are some actual standards which are referring to IEC-TR-62380.
SN 29500 is a reliability prediction standard developed by Siemens and is widely used in German-speaking regions, but is internationally recognized. It gives a good overview of the reliability prediction calculation for electromechanical components like switches, relays and connectors. The linear ICs are detailed and are represented by different sub-groups like operational amplifiers, voltage regulators etc. The standard has a simple structure without many textual parts. The disadvantage of the SN 29500 is the poor coverage of the environmental influence compared to IEC-TR-62380. The fact that the SN 29500 standard consists of 12 different documents with different revision levels (2004 – 2011) makes it difficult to judge the status against the latest technology.
IEC 61709:2017 is a guidance on the use of the failure rate date for reliability prediction. This standard shows how to construct a component failure database that can be used with stress models. It doesn’t provide base failure rates for components, but models for prediction. IEC 61709:2017 was presented as a merger of the IEC 61709:2011 version & the IEC TR 62380:2004 standard. However, in my opinion, it is more a derivation of SN 29500 standard. The other way around the SN 29500, is an IEC 61709 version ready for use in practice with given base failure rates.
FIDES Guide 2009 is a standard for reliability methodologies for electronic systems developed by French Industries. It was developed by analysing data from various industry sources, including military and aviation, and focuses on realistic reliability prediction. This means that FIDES is using the management approach for assessing failure rates. The standard is more quality management related and uses questionnaires and audits to assess and evaluate the influencing factors for failure rate calculation. This includes the evaluation of maturity of the component manufacturer, production process and final product.
Due to the management approach and the long list of the audit questions, FIDES 2009 is not always well accepted by the Engineers.
What standard should I use?
The selecting of the most appropriate analysis approach should be done based on organization needs, their design processes, technologies used and their products. IEC TR 62380 and SN 29500 are more supported with hard parameters and fixed base failure rate with a clear calculation process, but with missing detailed information how the calculation process was evaluated. Some doubt if this approach is still state of the art due to the fact that both standards are older now.
IEC 61709 is more or less a guideline which shows you potential failure sources and how to evaluate the rates, without hard numbers. FIDES 2009 can be helpful to improve and control the reliability throughout the life cycle. In addition to technological and physical factors, it considers the process factors contributing to reliability.
ISO 26262, the standard for functional safety in automotive industry is referring to all three reliability standards mentioned above and has incorporated the reliability prediction calculation methods of IEC-TR_62380 in own clauses. There are also other prediction standards like MIL HDBK 217 (military standard) mentioned in ISO 26262 but are not the focus of this blog due to old publication dates or of no relevance for hardware & semiconductor development.
So, of course it’s up to you which standard you want to use in the design phase of your product, but what can be recommended is to use a software tool for reliability prediction. There are different tools on the market that can be applied to different standards, do your homework to know which is right for you. This is a good way to compare the different calculation methods and to decide which reliability prediction results should be applied for the design process of the product.
I hope I have helped you to get a better understanding of that topic by giving you an insider’s view into reliability engineering. If you need support during integration of reliability engineering process, Lorit Consultancy GmbH is looking forward to supporting you on your way! Feel free to contact us: info@lorit-consultancy.com
By Dijaz Maric, Quality Management & Reliability Engineering Consultant
Do you want to learn more about reliability or Functional Safety requirements in the Automotive or Medical Device sector? We work remotely with you. Please contact us at info@lorit-consultancy.com for bespoke consultancy or join one of our upcoming online courses.