How reliable are you? Part 2: All Roads lead to Rome.
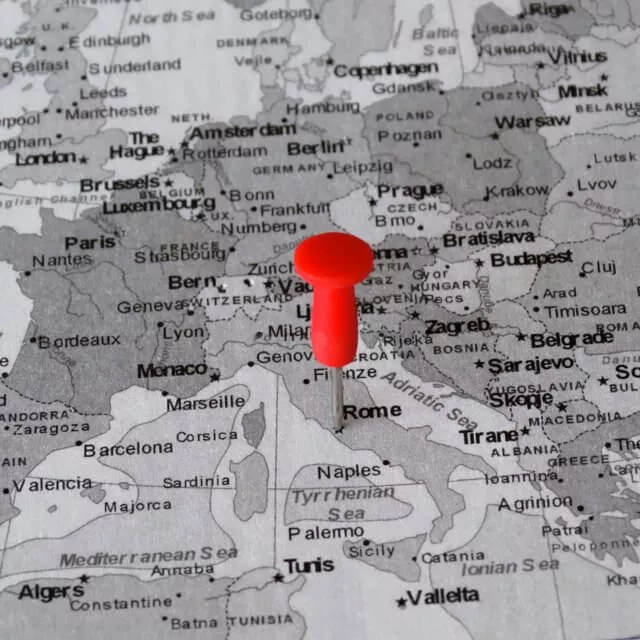
In the second part of my blog series (Part 1 was about reliability prediction analysis) I want to focus on different failures and calculation models that can be used for your reliability prediction, as well as about the different standards and handbooks for reliability.
Which failures are actually considered in the reliability prediction study? Experience and studies have shown that the error rate of the electrical components varies as a function of time and can be represented as a so-called bath tub curve, which should represent failure rates during the lifetime of a product. A product lifetime is divided into infant mortality period (early failures), period of useful life or maturity (mostly constant failure rate) and wear out period (wear failures).
Figure 1: Bathtub curve (Source: FIDES guide 2009)
At the beginning of a product lifetime, during the infant mortality period, the failure rate is varying and relatively high due to the fact that the setting up processes of the design and the debugging phase is ongoing. The reliability of the product is increasing with the time and a more or less constant failure is occurring which is in focus for the reliability prediction. The useful life period is represented by a constant failure rate. The constant failure rate is independent of the number of operational hours of the product (random failures). The failure rate is increasing again during the wear-out period with the number of hours of operation due to aging reasons.
The calculation of reliability parameters for the evaluation of electronic components and systems should usually only be carried out with the expected values that apply after the early failure phase at constant failure rate. The infant mortality and wear out periods are excluded (expect for a few cases) from prediction calculation. The infant mortality is representative for the development phase of a system and the wear-out phase is far removed from the periods of use. For these reasons, use of a constant failure rate for reliability prediction of electronic components or systems is the most relevant approach.
Reliability predictions are based on numerous assumptions, all of which need to be verified. As mentioned above, it is assumed that the failure rates are constant either for an unlimited period of operation in general case. Systematic failures due to errors of design, uses, production process issues are excluded from the reliability prediction and the focus is on the so-called random failures to which no specific root cause can be assigned.
To be able to conduct the failure rate calculation for prediction, you need to know the failure rate which corresponds to the most common operational and environment conditions, of course considering the different material and connection technology. This value is used as a reference failure rate (base or reference failure rate) which is further multiplied by a number of influencing factors.
ʎREF or ʎBASE
The reliability data for reference values are derived from different sources (field, manufacturers) and industries (military) and can be found at different reliability handbooks and standards.
Due to the fact that the electronic components and systems do not always operate under the reference conditions, the operating conditions have to be evaluated using models with different influencing stress factors.
There are different methods and guidelines (IEC-TR 62380, SN29600, FIDES etc.) how to calculate the failure rates for reliability prediction, but there is more or less a general approach to multiply the reference failure rates and influencing factors to get a failure rate in operating conditions.
ʎ = ʎREF x influencing factor 1 x influencing factor 2…..
It is important to mention that the standard calculation methods according the known reliability handbooks give you pessimistic or conservative results. In some cases, it is recommended to evaluate an alternative method to get a more realistic metric for the considered component or system (e.g. field data).
However, in the next part of the blog (How reliable are you? Part 3: Reliably ever after) we will continue to discuss about the different standards and handbooks for reliability, to compare the advantages/disadvantages of some of them and how to use them in practice.
By Dijaz Maric, Quality Management & Reliability Engineering Consultant
Do you want to learn more about reliability or Functional Safety requirements in the Automotive or Medical Device sector? We work remotely with you. Please contact us at info@lorit-consultancy.com for bespoke consultancy or join one of our upcoming online courses.