IATF 16949:2016 – Part 3: Outsourced electronic design/development processes
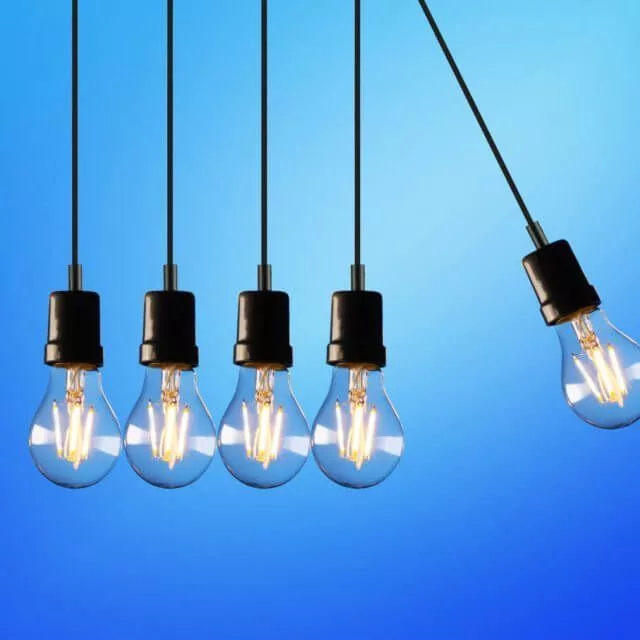
In the final part of this blog series, we are talking about the supplier management according to IATF 16949 and reference to external development processes. (Please find the IATF 16949 Blog Part 2 here and Part 1 here.)
Since a large number of subsystems are often created by suppliers, an efficient supplier management is necessary for the actual manufacturer of the product since they alone are responsible for the function of the delivered components in the overall system. In IATF 16949, the following is defined in the supplier selection process and supplier management and must be performed by the organization:
As mentioned in part 1 of the blog, the organization requires its suppliers of automotive products and services to develop, implement and improve an ISO 9001 certified QM system, ultimately with the goal of becoming certified under IATF 16949 standard of the automotive industry.
Controllers and other electronic components are designed and manufactured by many different suppliers in the automotive industry. These in turn, have an extensive supplier network. However, the functionality of all electronic components is only achieved by a compatible behavior of all components in an item or system. This must already be taken into account in the starting or requirements phase of the development projects.
At the beginning, the requirements of the development process are not precise or are very often incomplete. Especially in the case of distributed development, requirements which emerge later during the development process and have an impact on the requirements of their own development must be taken into account and well controlled. New insights results often in new requirements to repeat changes through the development process. Changing requirements or discovering errors during the development process lead to time- and cost-intensive iteration loops. If these occur in advanced phases, then the complete development process must sometimes be repeated several times.
One of the most important points in the supplier management is the transferring of the requirements throughout the complete supply chain. It’s not enough to just provide all requirements via e-mail or a transferring portal, joint reviews should be performed to have a common understanding on each side. The best approach in external provided development processes would be to organize regular meetings or even better to implement the external team in their own project team and project management structure to have an optimal control of the project and development phase.
If we take a look on the clause 8, chapter 4.1.1 in the IATF 16949 standard (information for external providers), the following is defined:
The organization must pass on all applicable legal and regulatory requirements as well as all product and process related characteristics to its suppliers. Subcontractors must be required to pass on all applicable requirements along the supply chain to the actual place of manufacture.
The focus here should be on the critical characteristics which are specified by customer or safety requirements in case of safety related products. The IATF 16949 standard defines exactly how the special charcteristics have to be implemented, documented, marked and controlled. To understand and keep this process controlled at external development provider is quite complex, and needs an approach according to the IATF 16949 standard.
As you can see, all important stakeholders have to be involved in the development process. Due to the many requirements in the automotive industry, it makes sense if all stakeholders and additionally the development service providers for HW and SW have introduced a uniform QMS according to IATF 16949. This facilitates communication, prevents errors in the development phase and increases customer satisfaction, thus increasing the reputation of the industry.
By Dijaz Maric, Quality Management & Reliability Engineering Consultant
You want to learn more about an internationally recognized Quality Management System (QMS) which enhances organisational performance, customer satisfaction and gives your organisation a competitive advantage? Then join one of our upcoming IATF 16949 training courses. You can find more information here.