Implementation of a QM system – the journey is the destination
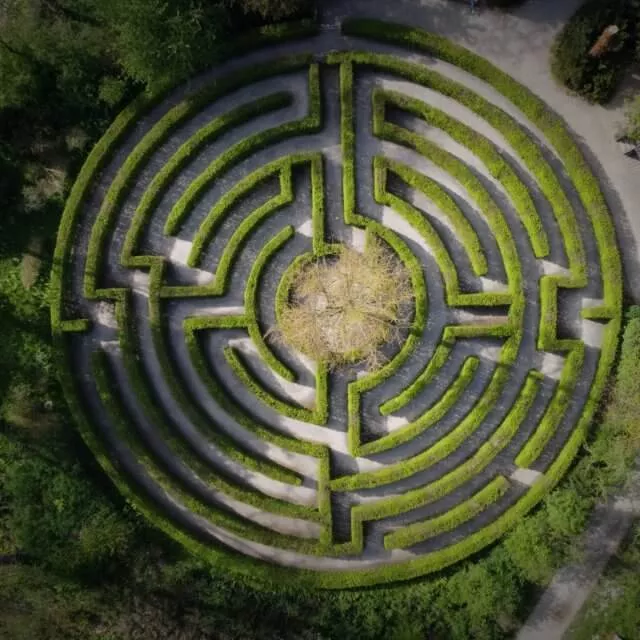
In the second part of our blog series on certification of quality management systems (Part 1: Cross Sector Quality Management), I would like to go deeper into the details of the process itself. What potential difficulties can occur during the implementation phases? And what approaches to problem-solving exist? Here are some practical tips from my many years of working with QM systems.
As with every project, the planning phase (quality planning) is very important for the implementation of a QMS. First, the current situation must be evaluated. The key word here is process documentation: What processes are already in place? What needs to be adjusted or improved? What areas are still not covered at all? Here it is advisable to have an experienced individual or organisation perform a gap analysis.
Following the gap analysis and identification of the ‘weak points’, the concrete planning phase starts: Who does what, when, how and with what? The resources required to reach the targets must be determined and then also made available. Personnel resources are a particular topic of discussion in many companies. Implementation or certification of a QMS requires time and a certain amount of effort, and this should not be taken lightly. For this reason, it is particularly important to plan things the right way. ISO 13485:2016 (Medical Devices – Quality Management Systems), for example, requires that a Management Representative be designated. The person in this role could – regardless of the quality management standard – take responsibility for monitoring the progress of the implementation and, if necessary, taking action.
During the planning phase, the ‘core’ and ‘supporting’ processes should be identified. The core processes are processes in the day-to-day business that create value. Supporting processes do not create value directly, but are of great importance to the execution or support of the core processes.
After the core and supporting processes have been identified, they must be documented. Either the existing processes can be documented or the processes can be replanned. The structure and process flows are determined and recorded on paper (nowadays usually in electronic form of course). Document and change management play a very important role here. The relationship between the documentation and the processes should be discernible to any employee at any time.
ISO 9001:2015 no longer requires a quality management handbook, it is sufficient to compile the documents in multiple files in an intranet or on the company platform. The basic idea of a QM manual was/is to ensure a quick overview of the management processes and their interfaces, the company strategy etc., primarily for new employees or external auditors. In the medical and automobile sectors, this document is still explicitly required.
Before you can implement a QMS in accordance with one of the standards mentioned in this blog series (ISO 9001, ISO 13485, IATF 16949), there must be a clear, strong management commitment! Quite frankly, if management is not behind the strategic decision to implement a QMS, then it will be essentially impossible to carry out. Resources are then often lacking, planned measures are not implemented, there is no sustainability etc. This means that management must show leadership and commitment with regard to the quality management system! Our experience has shown that this is often the fundamental problem both for startups and for larger companies.
Moreover, the QMS that is introduced must be put into practice. The company does not gain anything by defining processes and instructions but not practising them. Verification in the form of records (Change Management, Continuous Improvement etc.) – i.e. Quality Records – is very important in this context. Particular attention is also paid to these records in the context of the certification audit. The auditor can use them to easily get an impression of whether processes which have been implemented are also being followed. It is also about verifying conformity with requirements specified for the quality management system.
In the first blog in this series (Cross Sector Quality Management), we explained the different or similar certification processes for quality management systems. Audits are an important part of the certification process. It is important for the company to prepare well for them. But how best to do this?
This can be compared to school exams, where I would prepare myself for an exam by taking practice tests I had prepared myself. What I mean is that you should recognise the weak points in the system or in the process through internal audits and promptly implement corrective and improvement measures before the certification. The internal audit is also a kind of verification of previously implemented measures. Internal auditors should be persons with experience with QMS and relevant training. If there are no such persons are on staff at the company, it is advisable to obtain external support.
And now we come to the key message of this blog series: Quality must be sustainable! However, sustainability should not prevent changes taking place in a company, as change is the first step towards improvement.
By Dijaz Maric – Consultant Quality Management & Reliability Engineering
Are you looking for support with gap analysis, pre-audits and the certification process of your quality management system? With our many years of experience in the medical technology and automotive industry, we are your competent partner for the tasks to be mastered. Please contact us at info@lorit-consultancy.com