The VDA maturity level model – Planning & Realisation of Design Processes: Part 2
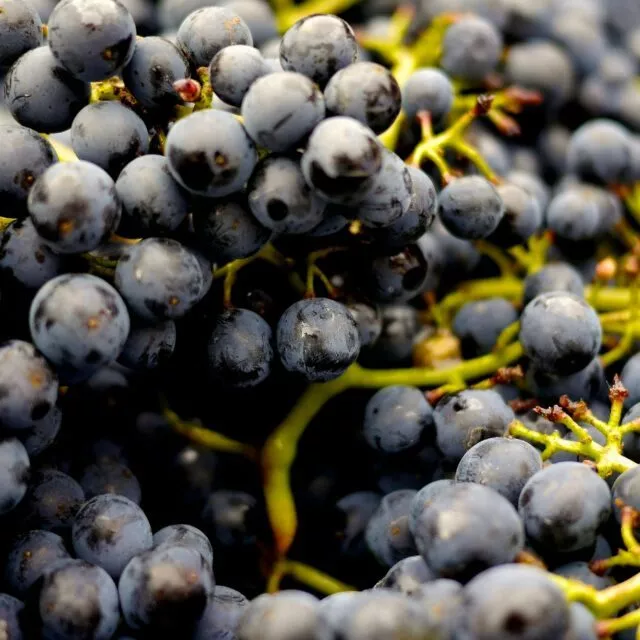
Among other things, a development process needs clearly defined, well-planned project management. In the first part of this blog series, we talked about the APQP approach, but we would also like to introduce the alternative, the VDA maturity level model.
The VDA maturity level assurance model stems from the quality management standard “VDA – Product creation – Maturity level assurance for new parts” and was last published in 2009 in its second edition. The aim of VDA maturity level assurance is to achieve and continuously improve the quality of new products in the automotive industry. This method consists of eight phases, the maturity levels ML0 to ML7, which ensure quality assurance from product maturity to SOP (start of production). As with APQP, all stakeholders within an organisation and, if required, throughout the supply chain are involved. Maturity level assurance creates a common understanding of definitions and contents and leads to the early detection of errors and deviations from project goals and enables early measures to stay on the right course.
The maturity level assurance model starts with ML0 in the concept phase and ends with ML7 after SOP. Each maturity level describes the status of goal achievement in terms of product, process and project maturity at the agreed milestones. In terms of product development, the focus is on phases ML0 to ML5. Maturity levels are usually based on the project schedule and can be easily integrated into the customers’ product realisation processes. VDA maturity level assurance provides you with all of the necessary information to evaluate the milestone in the milestone meetings.
The picture below shows an overview of the maturity levels with a selection of associated indicators. Standardised measurement criteria are assigned to the maturity indicators.
Dijaz Maric, QM & Reliability Engineering Consultant
Looking to enhance your automotive development processes? We support suppliers with ISO 26262, ASPICE, and automotive functional safety consultancy. Contact us at info@lorit-consultancy.com or explore our upcoming training sessions.
Learn moreThe scope of the maturity content is classified and prioritised at the start of the project. This content will be delivered by the suppliers to the customer at each stage of the supply chain. Merging product and supplier risk then leads to the classification of overall risk (ML2).
Maturity assurance is handled according to the risk classification in three different application levels (Figure 2).
Each maturity level is assigned a set of specific measurement criteria that are defined at the start of the project by the project team and also between the customer and supplier. All measurement criteria must be formulated in such a way that they can be clearly answered with a “yes” or “no”. Each individual measurement criterion is evaluated with a traffic light colour (red, yellow or green). The assessment criteria are consequently defined:
When carrying out the assessment using the maturity traffic light, defined rules for overall assessment, due dates, changes, red assessments, open measures, etc. must be observed and applied.
After completion of the assessment, regular status reports must be prepared and reviewed in the project team in order to be able to control the project.
With VDA maturity level assurance, all of the necessary information is presented in the milestone meetings to be able to evaluate the milestone. Even members of the decision-making bodies who are only marginally familiar with the project can thus objectively assess the milestones. This allows definitive decisions to be made based on the project documentation – assess, analyse and improve.
Issues can occur if project reviews (project closures) are not carried out consistently enough, or if the results of the project review are not taken into account in follow-up projects. Therefore, proper implementation and documentation of project reviews are essential.
VDA MLA is mainly found in German-speaking countries, but APQP is better known internationally and is becoming more important due to growing markets in Asia, for example. The APQP approach has proven so successful that the German automotive industry is also increasingly following this procedure.
Both VDA maturity assurance and APQP are project management methods or tools of and cannot, of course, completely replace it. By applying these methods, cooperation between customers, suppliers and partners is improved during the development phase and common goals are achieved more easily. A prerequisite for this is the involvement of qualified employees in these processes.
By Dijaz Maric, Quality Management & Reliability Engineering Consultant
Do you want to learn more about the implementation of IATF 16949, ISO 26262 or any other standard in the Automotive or Medical Device sector? We offer expert guidance on functional safety and regulatory compliance. Please contact us at info@lorit-consultancy.com for bespoke consultancy or join one of our upcoming online courses.