ISO 26262 Part 11 – Dependent Failure Analysis (DFA) – Part 3
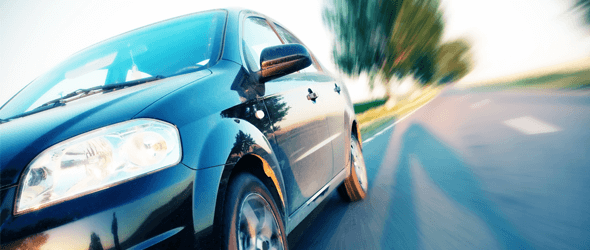
In our 3rd and final part of the ISO 26262 – Part 11 blog series (Read Part 1: Introduction to Part 11 here and Part 2: Base Failure Rates here), we look at the additional information added to support semiconductor manufacturers assess dependent failures in integrated circuits.
The DFA section of part 11 provides guidelines for the identification and analysis of possible common cause and cascading failures between given elements, the assessment of their risk of violating a safety goal (or derived safety requirements) and the definition of safety measures to mitigate such risk if necessary. This is done to evaluate potential safety concept weaknesses and to provide evidence of the fulfilment of requirements concerning independence or freedom from interference identified during coexistence of elements analysis.
As in keeping with other parts of the second edition of ISO 26262, the definition of dependent failures initiators (DFI) has been significantly enhanced. Using 7 categories of potential causes, typical dependent failures are listed.
Alastair Walker, Consultant
Need practical insights on ISO 26262 for E/E systems?
Our training courses and consultancy services support your team with implementation, safety lifecycle activities, and project-specific challenges. Use our contact form to share your thoughts and difficulties with us.
The process of analysing dependent failures is supported by workflow indicated in Figure 1. This workflow helps identify the main activities to understand the independence and freedom from interference when assessing the architecture and safety mechanisms.
As in the case of discrete circuits, the identification of the DFI is a key activity in assessing the ‘quality’ of architecture. The checklists of typical dependent failures help steer teams in this activity, but also as indicated in Figure 1 this process can be enhanced by crosschecking dependent failure mechanisms identified during quantitative analysis i.e. hardware metrics from part 5 of ISO 26262.
As is always the case in such activities, the end goal is to verify the effectiveness of any safety mechanism identified and implemented during the process. Techniques such as fault tree analysis, FMEA, fault injection and design rules are listed.
The steps identified for DFA in part 11 are not only helpful for semiconductor designers, they also provide very useful additional information for designers of discrete circuits.
Part 11 of ISO 26262 continues to expand valuable guidance for semiconductor manufacturers, particularly in assessing dependent failures. While originally tailored to complex integrated circuits, many of the methods and insights are equally applicable to discrete circuit design. With practical workflows, clear initiator categories, and established analysis techniques, this section supports more robust safety architectures and highlights how far the standard has evolved in supporting hardware-level safety.
Want to deepen your understanding of ISO 26262 for E/E systems?
Join one of our upcoming training courses or ask us how we can support you in strengthening functional safety, boosting performance, and gaining a competitive edge.